Expert Predictive Maintenance Integration to Increase Equipment Uptime
By adopting a predictive maintenance approach, marine operators can enhance vessel performance, safety, and efficiency. This strategy ensures timely maintenance, reduces downtime, and minimizes costs, leading to more reliable and sustainable maritime operations.
Implementing a predictive maintenance strategy for marine vessels can significantly reduce downtime, lower maintenance costs, and enhance operational efficiency. By utilizing advanced analytics and condition monitoring, marine operators can detect potential issues before they lead to equipment failures.
Predictive Assets Analytics: Predictive maintenance leverages data collected from existing onboard sensors and systems. Through machine learning and advanced pattern recognition, unique operational profiles for each asset are created. This process takes into account continuously changing loading, ambient, and operational conditions, enabling the system to monitor actual performance against model predictions and identify deviations in equipment behavior well before a failure occurs.
Early Warning and Fault Diagnostics: When an early warning notification is generated, predictive maintenance systems provide advanced fault diagnostics to help pinpoint the cause. This approach allows for proactive maintenance planning, reducing the risk of costly and potentially catastrophic failures, enhancing safety, and ensuring maintenance activities are strategically prioritized.
Transforming Maintenance Strategy: Transitioning from reactive to predictive maintenance maximizes economic returns on critical assets. This strategy helps marine operators reduce unplanned downtime, lower maintenance costs, and improve the reliability and efficiency of their vessels.
Condition Monitoring: Predictive maintenance relies on condition monitoring, using various measurements to assess the health of equipment such as motors, pumps, and generators. Factors like power consumption, vibrations, and temperature are continuously monitored to detect potential issues.
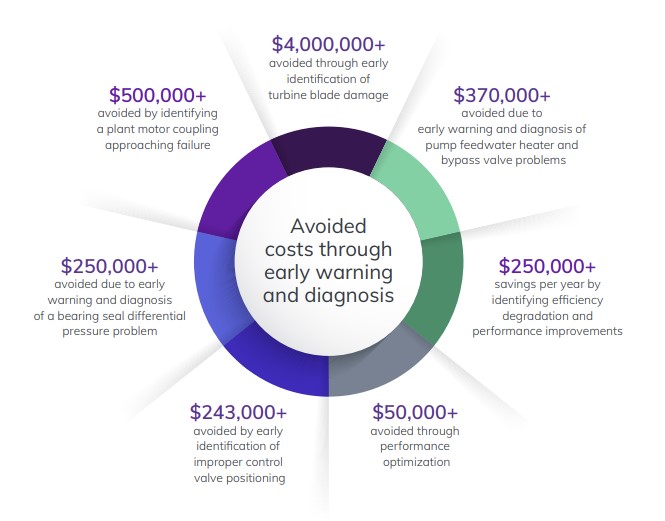
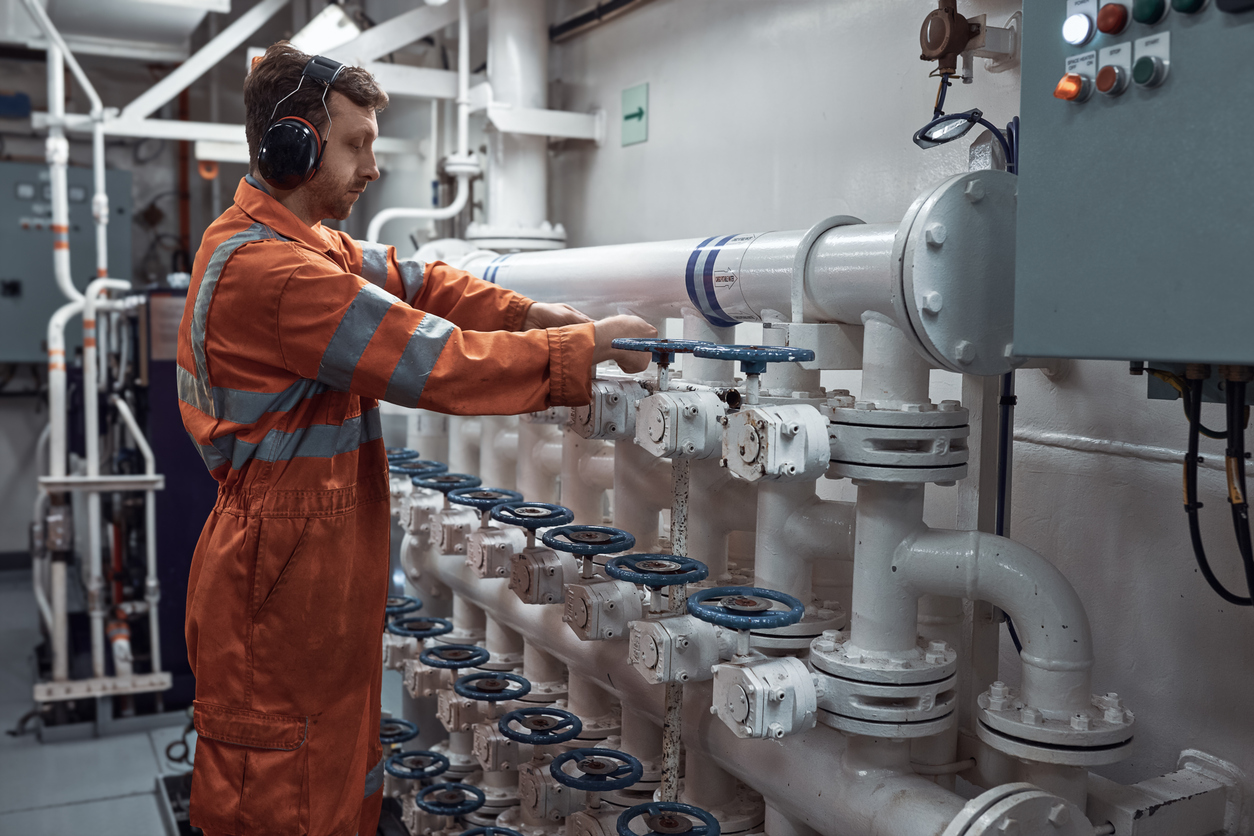
